Autor: Brian Owens
Prelazak sa automobila na benzin i dizel na električna vozila je jedan od načina da se smanji emisija ugljenika, ali proizvodnja litijum-jonskih baterija koje napajaju ta EV može sama po sebi biti energetski intenzivan i zagađujući proces. Sada su istraživači na Univerzitetu Dalhousie razvili proizvodni proces koji je jeftiniji i zeleniji.
„Izrada litijum-jonskog katodnog materijala zahteva mnogo energije i vode, i proizvodi otpad. To ima najveći uticaj na životnu sredinu, posebno na CO2 otisak ove baterije“, kaže dr Mark Obrovac, profesor na odeljenjima Hemija i Fizika i nauka o atmosferi Univerziteta Dalhousie.
„Želeli smo da vidimo da li postoje ekološki prihvatljiviji i održiviji – i jeftiniji – načini za proizvodnju ovih materijala.“
Većina baterija električnih vozila koristi litijum nikl mangan kobalt oksid (NMC), sa elementima pomešanim u kristalnoj strukturi katode. Obično se prave tako što se elementi rastvaraju u vodi, a zatim koriste kristali koji se formiraju kada se elementi spoje kao čvrsta supstanca.
Za taj proces je potrebno mnogo vode—koja se zatim mora obraditi da bi se očistila—i energije, koja je glavni izvor troškova i ugljeničnog otiska baterija. Koristeći kanadski izvor svetlosti (CLS – Canadian Light Source) na Univerzitetu u Saskačevanu, Obrovac i njegov tim su istraživali da li bi mogli da koriste potpuno suvi proces da bi dobili iste rezultate uz uštedu energije, vode i novca.
Njihov rad je objavljen u dva rada, u ACS Omega i Journal of the Electrochemical Society
„Hteli smo da vidimo, da li može da se dobije isti kvalitet ako se uzmu suvi materijali i kombinuju se koristeći jednostavne procese koji postoje u svakoj velikoj fabrici i zagreju se“, kaže on. „Pod kojim uslovima to može da se uradi da bi se dobio materijal komercijalnog kvaliteta a da se izostavi voda i izbegne otpadni materijal?“
Katode napravljene od suvih materijala ponekad nisu tako homogene kao one koje se prave u vodi, pa je tim isprobao različite metode koristeći različite okside i režime grejanja pod različitim temperaturama i pritiscima kako bi utvrdio šta najbolje funkcioniše.
Koristili su Brockhouse snop u CLS-u da zavire unutar peći dok su pokušavali ove različite eksperimente, da vide šta se tačno dešava tokom procesa. „Ono što smo utvrdili je važna informacija o tome kako možemo da unapredimo proces tako da dobijemo katodni materijal višeg kvaliteta NMC tipa“, kaže Obrovac.
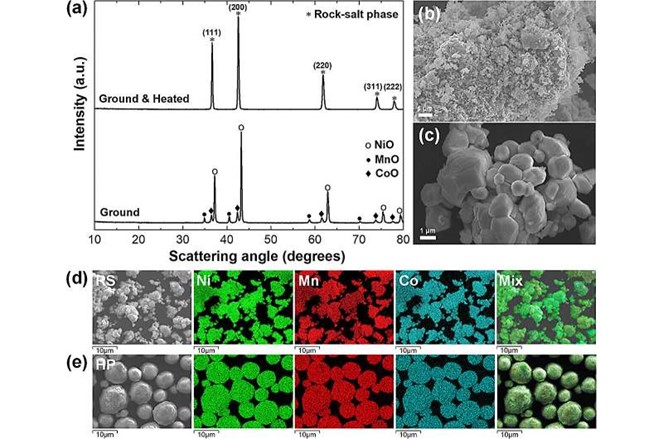
1 / 1(a) KSRD uzorci mešavine prahova NiO, MnO i CoO nakon 3 h mlevenja i posle zagrevanja da bi se formirali RS-prekurzori. SEM slike mešavine praha NiO, MnO i CoO nakon (b) 3 h mlevenja i (c) nakon zagrevanja da bi se formirao RS-prekursor. SEM slike i pridružena EDKS mapiranja Ni, Mn i Co za (d) RS-prekursor i (e) HP-prekursor.ACS Omega (2023). DOI: 10.1021/acsomega.3c08702
Najkvalitetnije katode koje su sada dostupne se prave od monokristala sa česticama prečnika oko 5 mikrona. Pažljivim prilagođavanjem početnih materijala i uslova u peći, tim Obrovca je uspeo da reprodukuje iste kvalitete potpuno suvim procesom, tako da su katodni materijali uporedivi sa najboljima na tržištu danas.
Obrovac je sklopio partnerstvo sa kompanijom NOVONIX sa sedištem u Novoj Škotskoj, koja koristi potpuno suve procese za proizvodnju katodnih materijala u pilotskom pogonu kompanije u Dartmutu. To postrojenje je u stanju da proizvodi 10 tona katodnog materijala godišnje, sa metodima koji nude po proceni 30% manje kapitalnih troškova od konvencionalnih (mokrih) metoda, 50% niže operativne troškove i koristi 25% manje energije, dok u procesu ne zahtevaju nikakvu vodu i generišu nula otpada.
„Ovo su velike brojke, to je velika promena u proizvodnji ovih baterijskih materijala“, kaže Obrovac. „To bi trebalo da rezultira jeftinijim baterijama u celini sa znatno manjim otiskom globalnog zagrevanja.“
Izvor: TechXplore